Case Study: Floored by the Results - Rio Saves National Retailer Days of Downtime with New Flooring System Installation
- bjw414
- Aug 1, 2024
- 2 min read
Updated: Aug 27, 2024
Leading food retailer reduces downtime, minimizes lost sales and improves safety by hiring RIO Flooring to re-surface floors in hundreds of its food-preparation areas nationwide.
The Company
Our customer is a US nationwide retailer with over 600 stores. Each store features multiple food-preparation areas, including bakeries, meat-prep areas, milk coolers, and food courts.
The Situation
The retailer faced significant wear and tear on their floors. These areas undergo constant use, with heavy equipment, carts, and trolleys causing the concrete to become porous, slippery, and difficult to clean. This not only posed a safety risk, but also affected operational efficiency.
The Solution
RIO Flooring specializes in providing high-quality flooring solutions, particularly for demanding retail, commercial and industrial environments. With expertise in installing and resurfacing floors in various settings, RIO Flooring is known for its durability, safety, and efficiency.
We consulted with the retailer to understand their issue in detail. Then we deployed a four-part remedy:
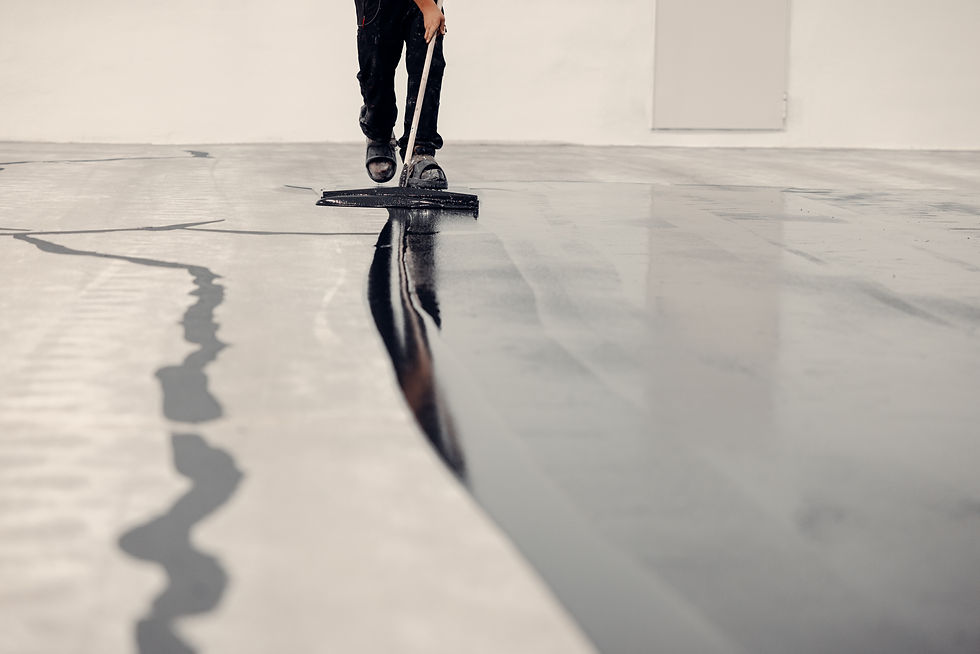
Floor Preparation: Removal of existing floor coatings down to the virgin concrete to ensure a strong bond.
Application of Urethane Cement: We applied Rio Crete with a broadcast aggregate for anti-slip properties. This cement mitigates moisture and withstands thermal cycling from hot water washdowns and temperature variations in freezers and bakeries.
Top Coat Application: We applied a methyl methacrylate (MMA) top coat, chosen for its high abrasion resistance, fast curing time (ready in one hour), and matte finish to hide imperfections.
Anti-Slip Aggregate: A 16/30 mesh size aggregate was used for its balance between providing texture and being easy to clean, essential for maintaining hygiene standards in food-preparation areas.
The Results
The solution provided by RIO Flooring yielded remarkable results:
Reduced Downtime: The new flooring system significantly reduced downtime. Projects of this scale typically take five days. But with RIO Flooring’s approach, we completed each area in three days—a 25% reduction in project time.
Rapid Return to Service: The MMA top coat allowed areas to be operational within an hour after application, compared with the 24-48 hours required for traditional coatings.
Cost Savings: The faster turnaround resulted in considerable cost savings. For the food court area alone, the retailer saved approximately $100,000 per day in lost revenue, translating to substantial financial benefits across multiple stores.
Enhanced Durability and Safety: The new floors are three-times harder than standard concrete, providing better impact resistance and a safer, non-slip surface that is easier to clean and maintain.
Long-Term Warranty: RIO Flooring offered a five-year performance guarantee, far exceeding the industry standard of a one-year warranty for manufacturer defects only.